May 07, 2021
MOLWED
Molweld es una empresa familiar ubicada en Cuarte de Huerva y especializada en la fabricación de moldes multicavidad pequeños y medianos de alta precisión y complejidad. La ventaja de sus soluciones técnicas innovadoras reside en garantizar el elevado volumen de ciclos que pueden soportar sin tener que ser reparadas (hasta dos millones), cumpliendo con las tolerancias y los acabados requeridos. Durante sus 20 años de vida, sus clientes han sabido apreciar el cuidado que Molweld pone en cada pieza y sus cortos plazos de entrega, valores que la diferencian frente a la feroz competencia asiática.
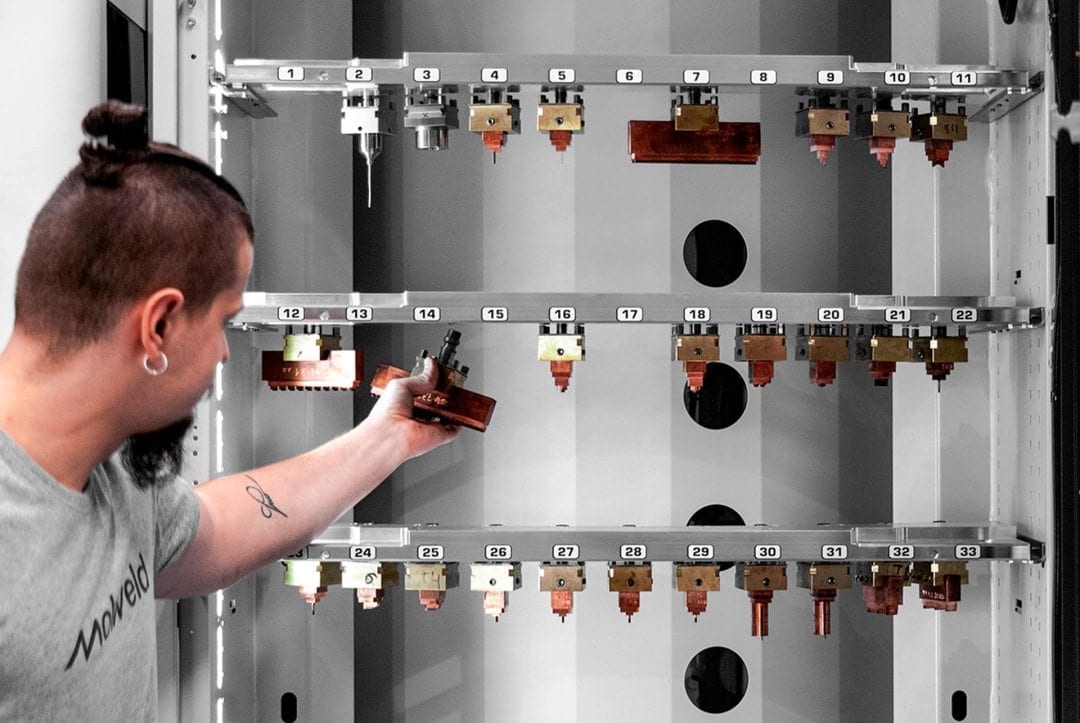
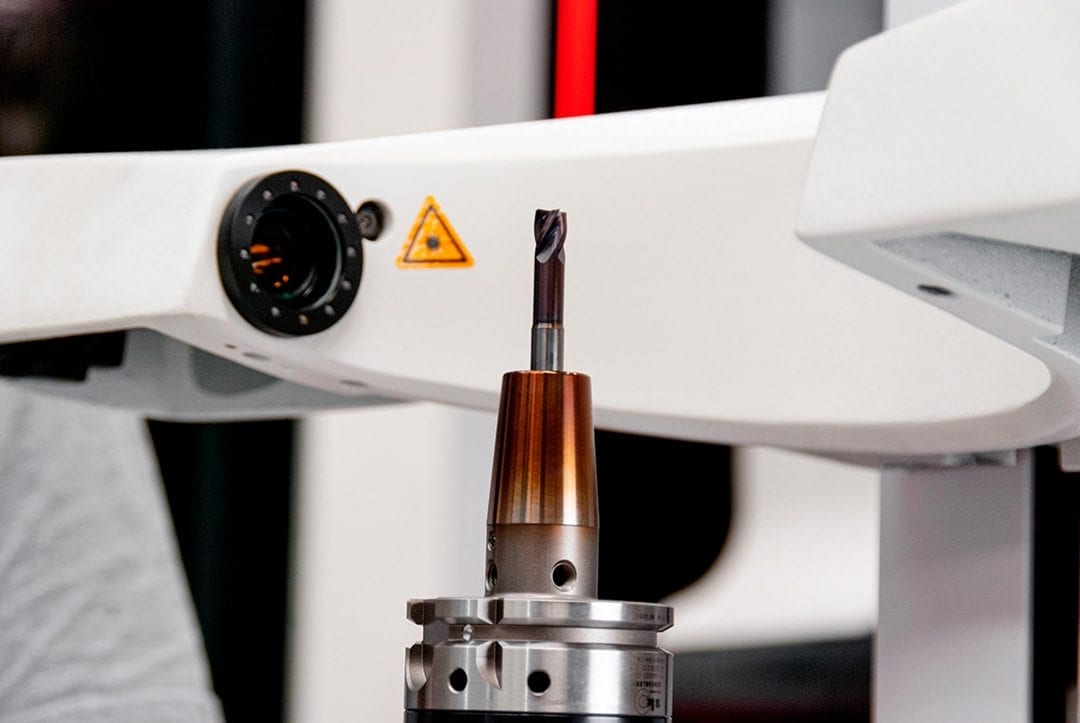
Sus moldes son el primer paso para fabricar piezas imprescindibles de automoción, como manguitos, retrovisores, mandos de control, juntas, componentes eléctricos o elementos decorativos, pero también de los sectores del menaje o los electrodomésticos de gama blanca. “No se ven pero son muy complicados. Nadie se imagina la cantidad de dedicación que requieren. Trabajamos para clientes de todos los tamaños e intentamos satisfacer sus peticiones, estamos abiertos a producir cualquier cosa para tiradas larguísimas”, afirma Juan Carlos Gracia, fundador de la empresa junto a su esposa, Susana Virgos. “Nuestro oficio es muy gratificante porque estamos constantemente haciendo cosas nuevas. Ponemos nuestro ingenio al servicio del cliente para ayudarle y darle ideas de cómo mejorar su producto, manteniendo una relación fluida y permanente”, destaca.
La firma aragonesa controla todo el proceso de fabricación, ya que no subcontrata ninguna fase de la producción del molde. En la calidad que ofrece es decisivo el papel que juegan las herramientas y los componentes que emplea, procedentes de Europa y que, por tanto, cumplen con los estrictos estándares que exige la industria del continente. “La utilización de componentes homologados nos garantiza poder identificar o descartar problemas surgidos por el material y nos facilita la realización de reparaciones y futuras adaptaciones del molde”, explica Gracia. “Nuestra precisión es máxima para poder hacer repuestos sin necesidad de tener el molde original en nuestras instalaciones”, añade.
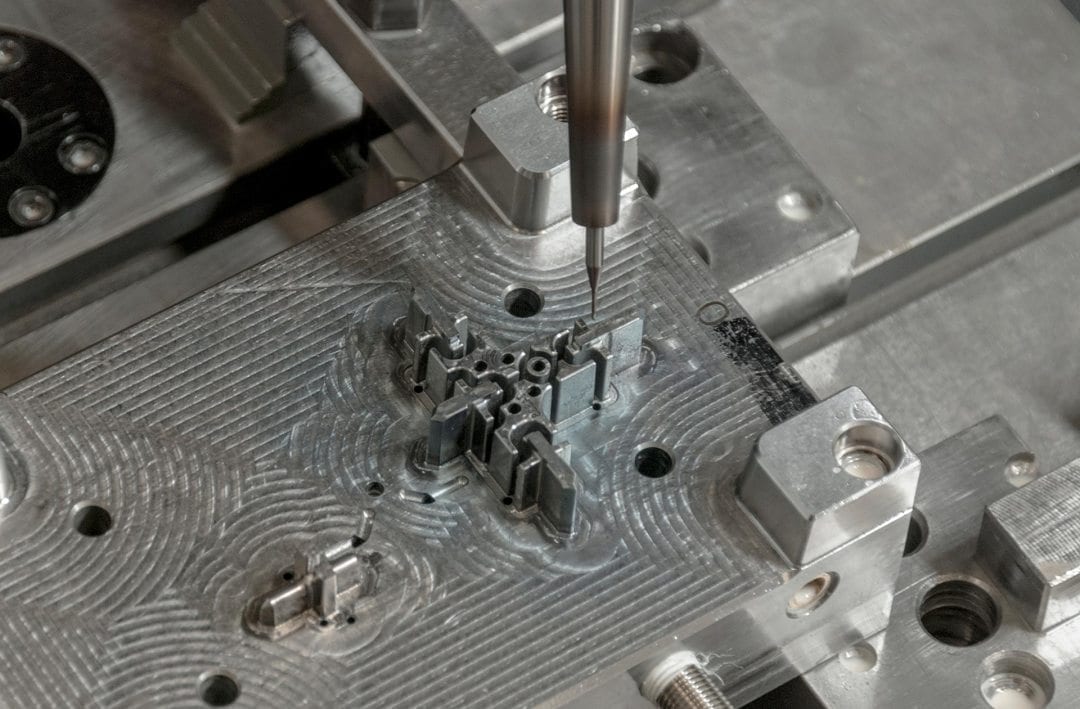

Además, han desarrollado una plataforma digital que permite a sus clientes poder hacer un seguimiento online de los moldes que están en proceso de fabricación. “A través de este sistema le otorgamos un control visual instantáneo de todos los proyectos que tengan en activo, pudiendo monitorear cada etapa del desarrollo del molde, acceder a imágenes y conocer el tiempo restante para su finalización”, describe Gracia. Esta tecnología forma parte de las inversiones con las que Molweld se refuerza periódicamente. “Desde que creamos la empresa, en 2001, todos los beneficios obtenidos se reinvierten”, afirma. Así, la firma acaba de incorporar un centro de mecanizado paletizado que reduce el tiempo entre cambio de placas, permitiendo trabajar las 24 horas, y un robot Erowa que lo conecta con las máquinas de erosión para poder almacenar y utilizar todos los electrodos que se fabrican directamente en máquina sin perder tiempo en cambiarlos manualmente. “Buscamos y probamos herramientas constantemente para optimizar nuestros tiempos de mecanizado y mejorar la calidad de nuestros acabados, logrando que la etapa final de ajuste sea mínima”, asegura.
Del mismo modo, todos sus centros de mecanizado tienen incorporado dentro de la propia máquina un software especializado de medición tridimensional, capaz de medir todos los puntos antes y después de cada mecanizado. “De esta forma nos aseguramos de que se respetan todas las medidas tridimensionales deseadas y conseguimos que siempre sean exactas, eliminando el factor de error humano en las distintas etapas del mecanizado”, subraya Gracia.
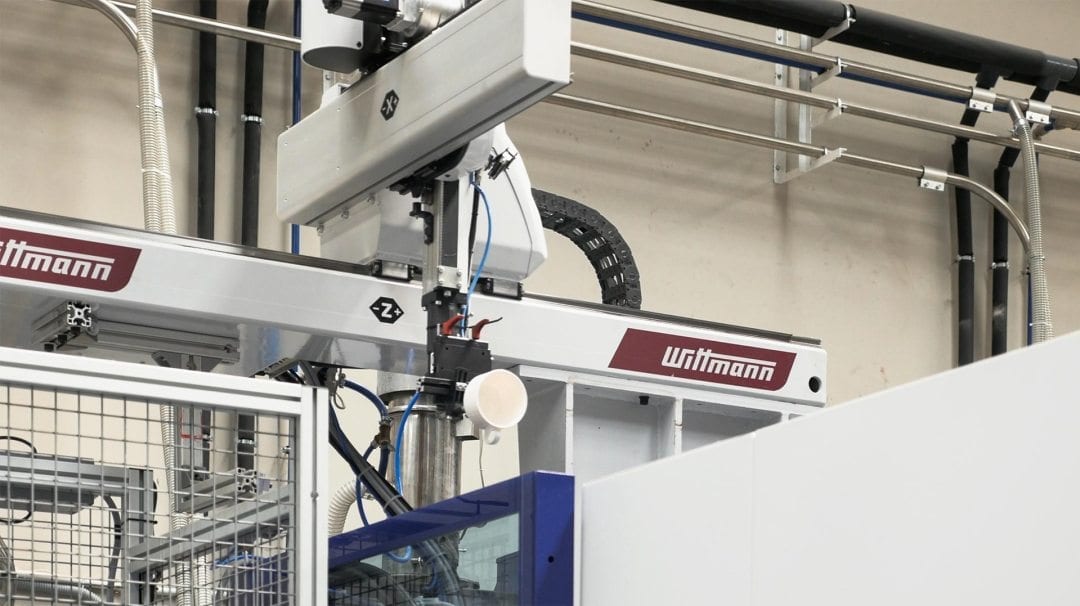
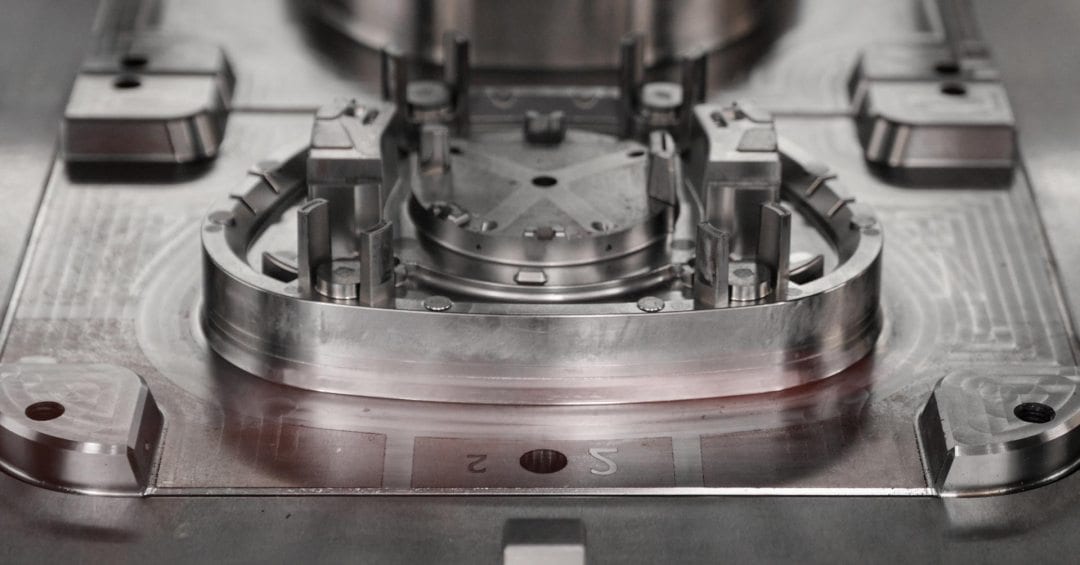
Esta estrategia de apuesta por la innovación, junto a la experiencia de dos décadas en el sector, dan como fruto plazos de entrega muy ajustados sin que la calidad en los materiales y la precisión se vean comprometidas. “Durante esta crisis sanitaria se nos presentó un proyecto urgente que consistía en fabricar un molde multicavidad para unas gafas de protección homologadas y lo logramos en 20 días”, relata el empresario zaragozano con orgullo.